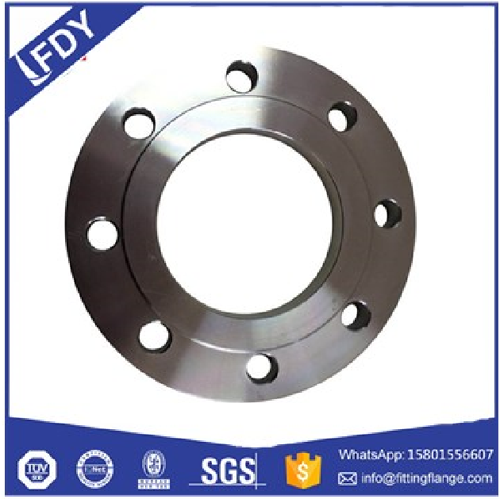
Abstract
Alloy steel flanges, as critical components in pipeline systems, play an indispensable role in modern industrial infrastructure. This paper systematically analyzes the multifunctional applications of alloy steel flanges by exploring their material properties, technical advantages, and practical uses across various industries. Through case studies and technical comparisons, this research highlights their irreplaceable value in high-demand engineering environments and forecasts their development trends in future industrial applications.
1. Introduction
In industrial pipeline systems, flanges serve as vital connecting components, responsible for ensuring structural integrity and leak-proof sealing. Alloy steel flanges, formed by alloying carbon steel with elements such as chromium, molybdenum, nickel, and vanadium, exhibit superior mechanical properties compared to conventional carbon steel flanges. These properties include high-temperature resistance, corrosion resistance, and pressure tolerance, making them essential in extreme working conditions. This paper aims to elaborate on the specific applications of alloy steel flanges in different industries and their technical advantages.
2. Material Properties and Technical Advantages of Alloy Steel Flanges
2.1 Key Alloying Elements and Their Functions
Chromium (Cr): Enhances corrosion resistance and oxidation resistance, particularly in acidic environments. For example, in Cr-Mo alloy steel flanges, chromium forms a dense oxide film on the surface to prevent medium erosion.
Molybdenum (Mo): Improves high-temperature strength and resistance to hydrogen corrosion. In hydrogenation reaction devices in the petrochemical industry, Mo-containing alloy steel flanges maintain structural stability at high temperatures (above 500°C).
Nickel (Ni): Enhances low-temperature toughness and corrosion resistance. Nickel-alloyed flanges are widely used in cryogenic pipelines (e.g., liquefied natural gas transport) to prevent brittle fracture.
Vanadium (V) and Tungsten (W): Act as grain refiners and strengtheners, improving the creep resistance of the material. In power plant superheater pipelines, V-W alloy steel flanges withstand long-term high-temperature and high-pressure conditions.
3. Industrial Applications of Alloy Steel Flanges
3.1 Petrochemical Industry
In petrochemical refining and chemical synthesis processes, pipelines often carry high-temperature/high-pressure media (e.g., crude oil, hydrogen, and sulfuric acid). For instance:
Hydrocracking Units: Use ASTM A182 F11/F22 alloy steel flanges, which withstand temperatures up to 550°C and hydrogen pressures exceeding 15 MPa, preventing hydrogen-induced cracking (HIC).
Sulfuric Acid Pipelines: Employ duplex stainless steel flanges (e.g., ASTM A182 F51), where the combination of chromium and molybdenum provides excellent resistance to sulfuric acid corrosion, with a service life 3-5 times longer than carbon steel flanges.
3.2 Power Industry
In thermal power and nuclear power plants, alloy steel flanges are critical for main steam pipelines and nuclear reactor cooling systems:
Ultra-Supercritical Power Plants: Use ASTM A335 P91/P92 alloy steel flanges, which exhibit creep rupture strength exceeding 100 MPa at 620°C, meeting the needs of ultra-high-temperature (600-650°C) and ultra-high-pressure (25-35 MPa) steam systems.
Nuclear Power Primary Circuits: Adopt low-carbon stainless steel flanges (e.g., ASTM A182 F316L), which resist chloride ion corrosion and radiation, ensuring long-term safe operation in nuclear environments.
3.3 Natural Gas and Offshore Engineering
In natural gas transmission and offshore platforms, alloy steel flanges face challenges such as low temperatures, high pressures, and salt spray corrosion:
LNG Terminals: Use ASTM A350 LF3 alloy steel flanges, which maintain ductility at -196°C, preventing brittle failure in liquefied natural gas pipelines.
Offshore Oil Pipelines: Employ super duplex stainless steel flanges (e.g., ASTM A182 F53), with a pitting corrosion resistance equivalent (PREN) exceeding 40, effectively resisting chloride ion corrosion in seawater.
3.4 Pharmaceutical and Food Industries
In hygienic pipelines requiring high corrosion resistance and cleanliness, such as pharmaceutical solvent pipelines and food processing lines, 316L stainless steel flanges (an austenitic alloy steel) are widely used. Their low carbon content and high molybdenum content prevent intergranular corrosion and ensure compliance with FDA hygiene standards.
4. Manufacturing Processes and Quality Control
4.1 Main Manufacturing Processes
Forging: High-performance alloy steel flanges (e.g., F91) are typically forged to refine the grain structure and improve mechanical properties. For example, multi-directional forging of P91 steel flanges reduces carbide segregation and enhances uniform performance.
Heat Treatment: Processes such as quenching and tempering (e.g., normalizing at 1050°C followed by tempering at 760°C for F22 steel) optimize the microstructure to achieve the desired strength-toughness balance.
Welding: Specialized welding procedures (e.g., low-heat-input welding with ERNiCrMo-3 filler metal for Inconel alloy flanges) are used to prevent heat-affected zone (HAZ) embrittlement.
4.2 Quality Assurance Standards
Non-Destructive Testing (NDT): 100% ultrasonic testing (UT) and magnetic particle testing (MT) are performed to detect internal defects (e.g., cracks, inclusions).
Pressure Testing: Flanges undergo hydrostatic testing at 1.5 times the design pressure (e.g., 22.5 MPa for a 15 MPa-rated flange) to ensure leak-tightness.
Material Certification: Compliance with standards such as ASME B16.5 (pipe flanges) and API 605 (large-diameter flanges) is verified through chemical composition analysis and mechanical property testing.
5. Challenges and Future Trends
5.1 Current Challenges
Material Cost: Alloy steel flanges are 2-5 times more expensive than carbon steel flanges, requiring cost optimization in large-scale projects.
Complex Fabrication: High alloy content increases the difficulty of hot working and welding, necessitating specialized equipment and technical expertise.
Environmental Requirements: Stringent emission standards (e.g., EU REACH) drive the development of lead-free and low-toxic alloy systems.
5.2 Development Trends
New Materials: Nano-alloyed steel flanges (e.g., adding rare earth elements) are being developed to further improve corrosion resistance and fatigue strength.
Additive Manufacturing: 3D printing of complex alloy structures (e.g., Inconel 718) enables near-net-shape production, reducing material waste by 30-50%.
Intelligent Monitoring: Integration of IoT sensors (e.g., strain gauges and corrosion sensors) into flanges allows real-time condition monitoring, predicting failures before they occur.
6. Conclusion
Alloy steel flanges are indispensable in modern industry due to their superior mechanical properties and environmental adaptability. From high-temperature petrochemical reactors to cryogenic LNG pipelines, their reliable performance ensures the safe and efficient operation of critical infrastructure. As industries advance toward higher temperatures, greater pressures, and stricter environmental standards, alloy steel flanges will continue to evolve through material innovation and process optimization, maintaining their core 地位 (core position) in global industrial development. Continuous technological breakthroughs in this field will further expand their application horizons, driving progress in energy, manufacturing, and other key sectors.